Go-to tips to improve industrial process.
Check out our useful guidelines for improving industrial processes, and see if your business is eligible for incentives to help cover the costs of switching to electric.
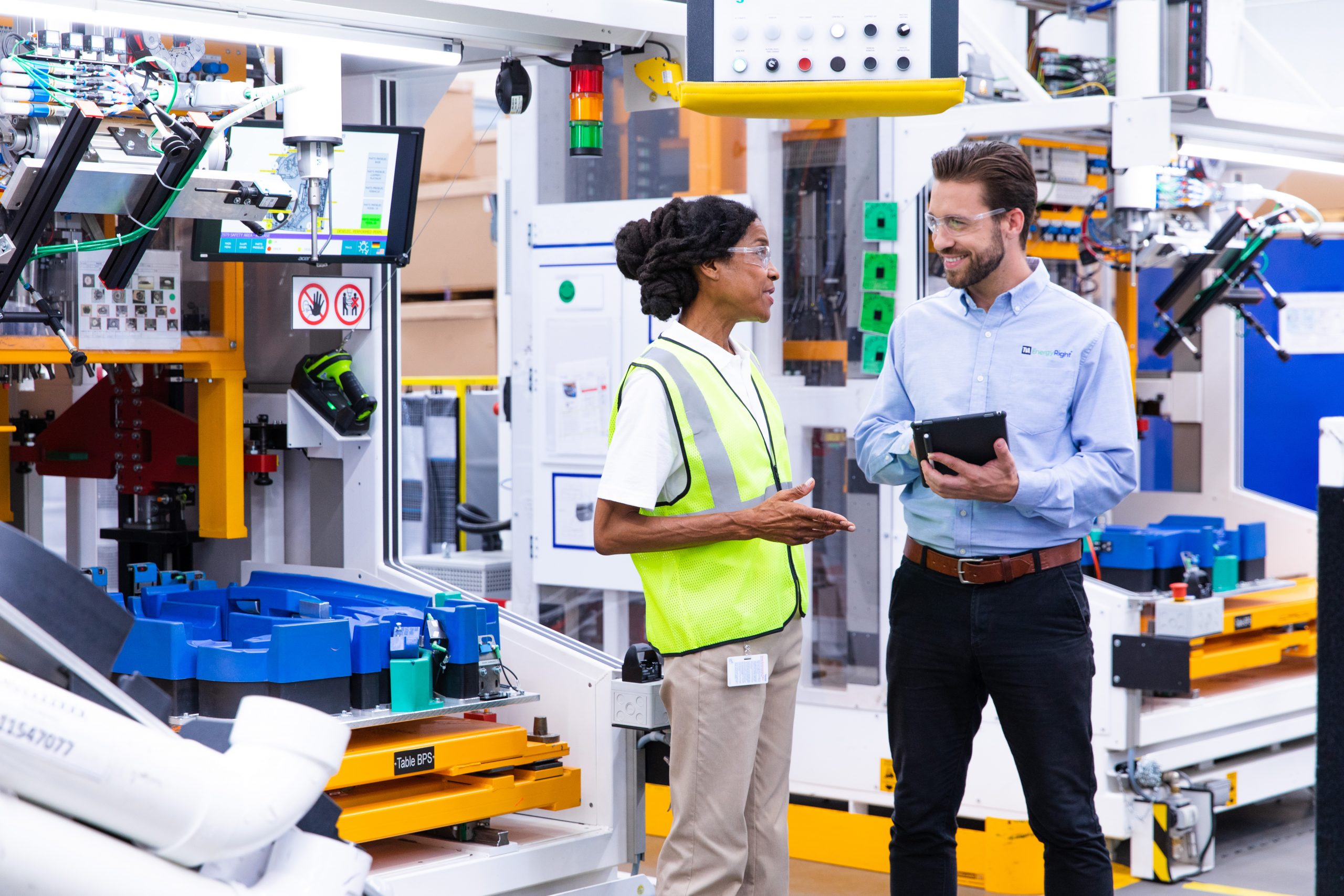
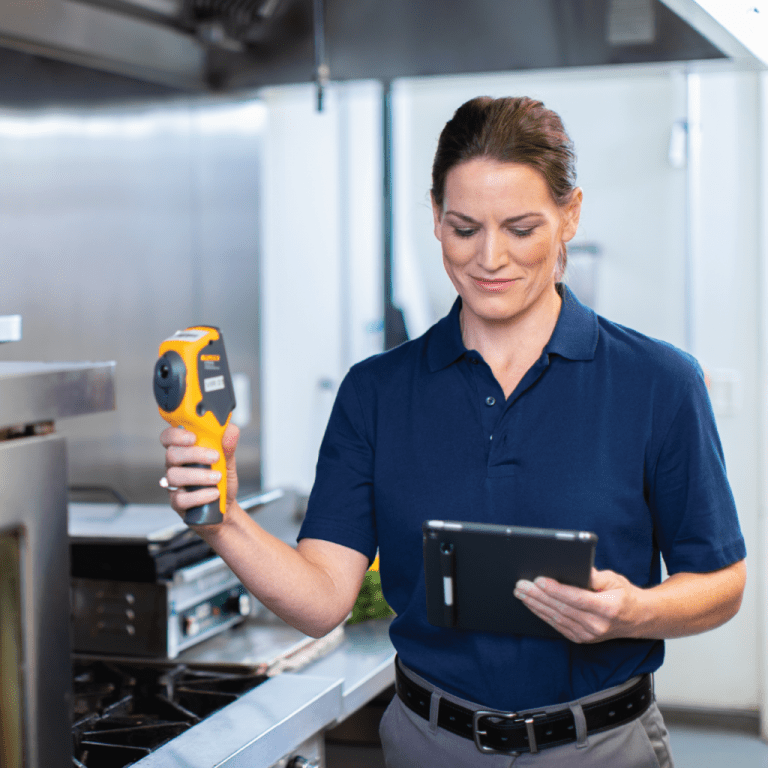
Making the most of motors.
Since motors drive so many industrial systems, it’s not enough to consider the energy efficiency of each individual motor. It’s most beneficial to your business to take a comprehensive systems approach that considers the entire motor system, the equipment they drive and the control system.
- Locate, identify and assess all motors in the facility, ensuring they’re properly installed.
- Document the specifications and conditions of each motor to create a system inventory.
- Collect information on potential repairs and changes to create a plan for increasing efficiency. Consider:
- Long-term costs—95% of a motor’s lifetime costs come from its energy consumption, not purchase or installation.
- Rewinding vs. replacement. It may be more cost-efficient to rewind an existing motor, but opt for the new motor if rewinding exceeds 60 percent of the cost of replacement.
- Adjustable-speed drives, which better match speed to load requirements and can produce energy savings up to 60 percent.
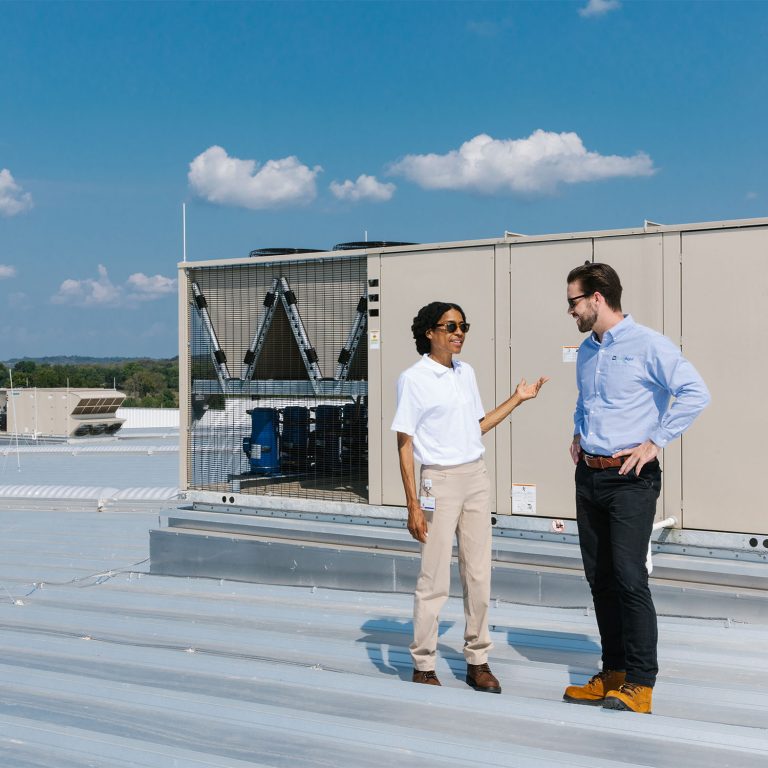
Perfecting the pump system.
Pumps are critical to any industrial process that involves moving liquid, whether for cleaning, circulating fluids or eliminating wastewater. To improve efficiency, we recommend:
- Replacing older pumps with high-efficiency pumps. A pump’s efficiency can drop 25% over time, and a newer pump could save up to 10% in energy costs.
- Considering multiple pumps for a variable-load system.
- Considering adjustable speed drives, which better match speed to load demand, where appropriate.
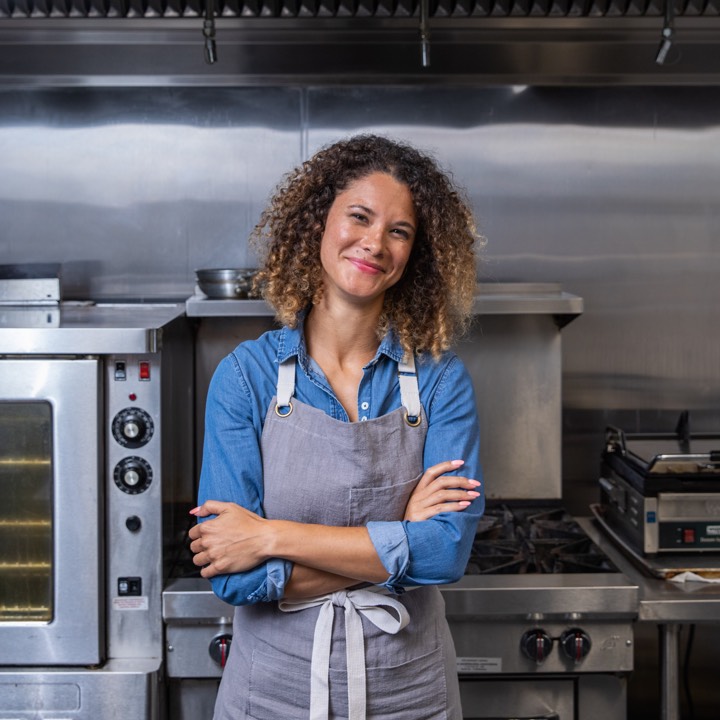
Keeping tabs on compressed air systems.
Compressed air systems are the least-efficient form of industrial energy, so finding alternatives is ultimately better for your business. Because of the low efficiency of these systems, investing in improvements can pay for itself in as little as a year. We recommend using these systems sparingly, and following these tips to maximize their operation:
- Make maintenance a priority to avoid air leakage, pressure variability, high temperatures, moisture problems and component contamination.
- Repair leaks to keep production capacity high and energy costs low.
- Always turn off unused compressed air systems immediately.
Additional incentives
See all the incentives available for different areas of your business.
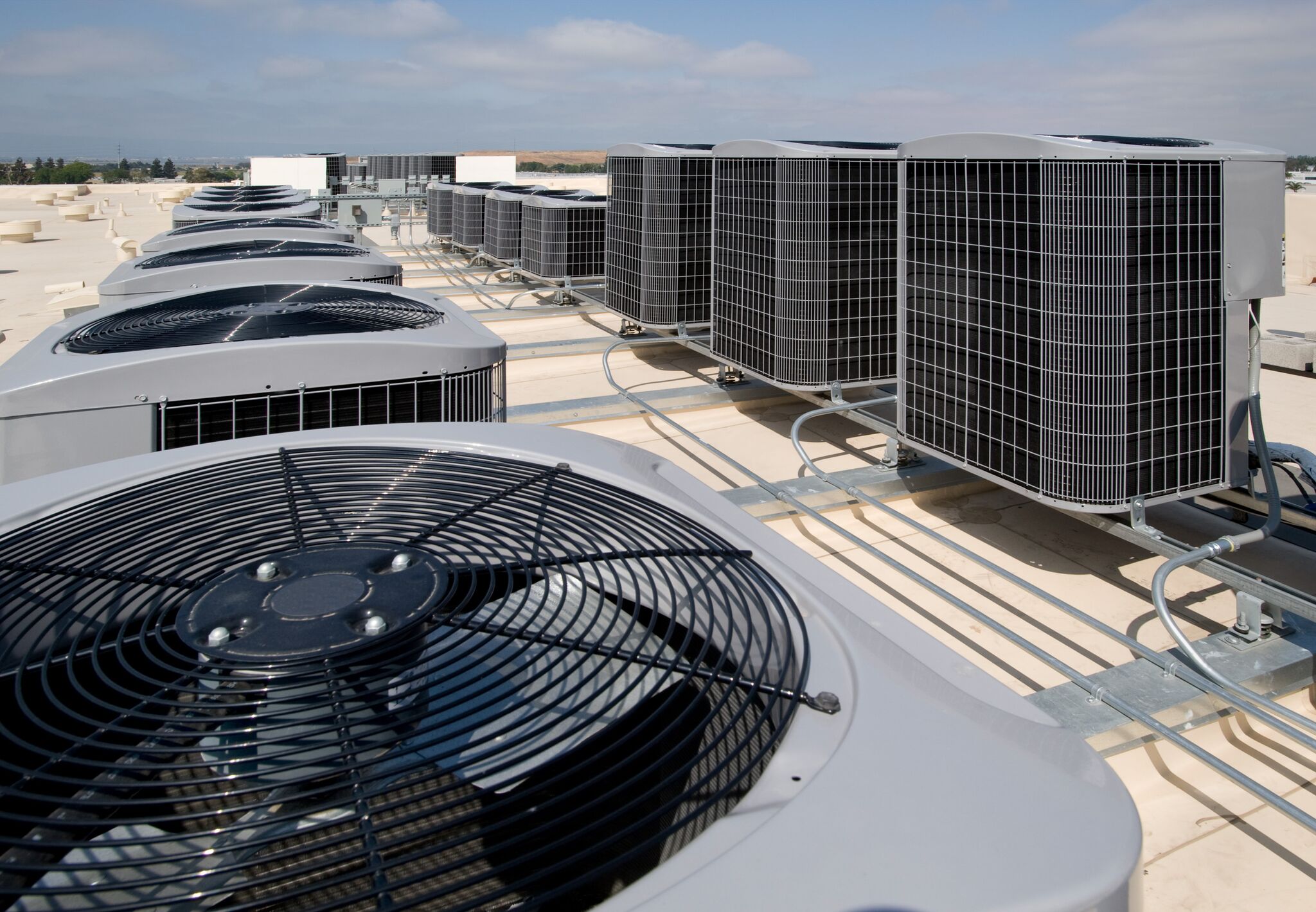